ANSI Pump Impellers In the ANSI pump world there are essentially 2 different choices for impellers; open (semi-open) and reverse vane. (I will hereafter refer to both the open and semi open designs simply as open.) True open impellers are not commonly used in industrial pumps because the demands of service require sufficient vane support (webbing or shrouds) to buttress the required torque loads and to maintain the relative geometric position of the vanes. Note: there is a closed impeller option for ANSI substituted in some rare cases. 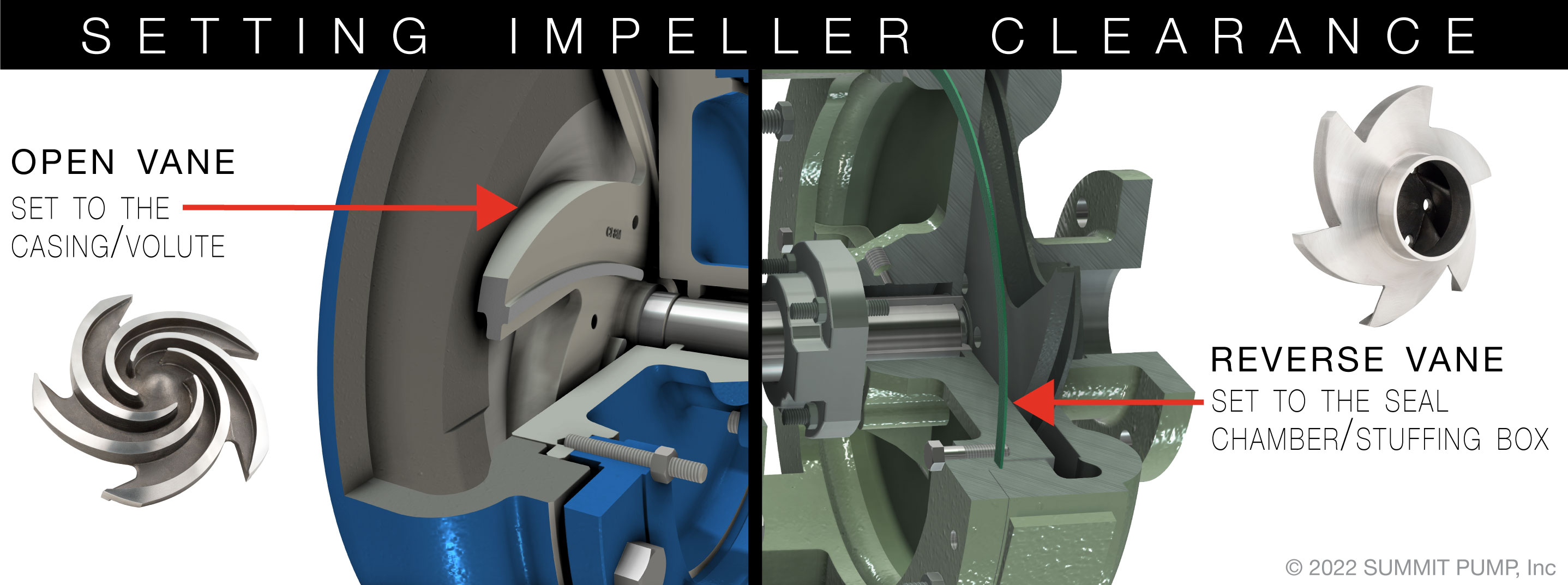 In general, the reverse vane impeller clearance is established to the stuffing box and the open impeller style is matched to the casing. Each design has its pros and cons. Considering all the possible pump application variables neither style is the overall winner. The requirements of each application should dictate the design choice. One Way or Another
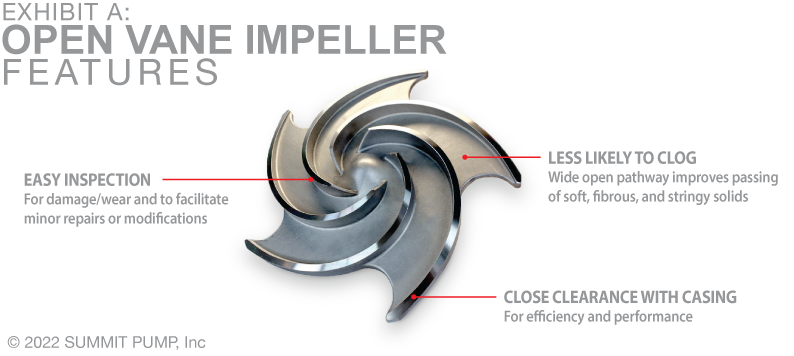 - Less likely to clog when solids are present and have the advantage of passing soft, fibrous, and stringy solids.
- Lend themselves to inspection for damage/wear and to facilitate minor repairs or modifications.
- Less costly to manufacture when compared to either fully closed and/or reverse vane impellers.
- Rely on a close clearance with the casing for efficiency and performance.
- Utilize the adjacent casing area for the primary wear area.
- Clearance can ostensibly be set on the bench (without the casing) but it must be checked/adjusted again for accuracy when placed in the casing.
- When initially and properly set, can be just as efficient as a closed impeller.
- Typically utilize rear pump out vanes to reduce the axial hydraulic thrust, but in some cases will also feature hydraulic balance holes (ports).
- The stuffing box pressure will typically be higher than a pump with a reverse vane impeller.
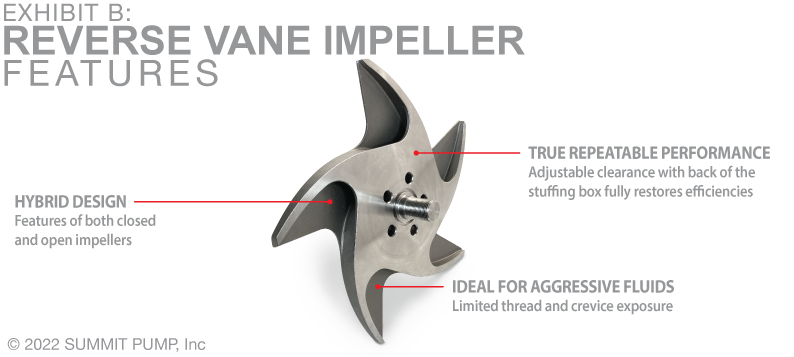 - Used for aggressive fluids like acids and corrosives because of limited thread and crevice exposure.
- Uniquely designed with features of both closed and open impellers.
- Rely on the adjustable clearance with the back of the impeller and stuffing box face (mechanical seal chamber) for efficiency and performance.
- Utilize the rear cover (stuffing box/mechanical seal chamber) as the primary wear area.
- Facilitates accurately adjusting the impeller on the work bench. That is, the pump does not need to be installed in the casing to accurately set the clearance.
- Clearance can easily be set using the micrometer style rear cover design feature when compared to the open impeller techniques (Subjective).
- Utilize balance holes to reduce the axial hydraulic thrust.
- Achieve true repeatable performance. Each time you reset the impeller clearance the pump performance returns to like new which includes the stuffing box pressure and the magnitude of axial thrust.
Closing Remarks
Reverse Vane Impellers There are claims that the reverse vane impeller requires less net positive suction head than open impellers for a given set of hydraulic conditions. We find this assertion unsubstantiated. Each individual application needs to be examined for its own merits. Reverse vane designs typically prove more practical with double mechanical seal applications because the seal pot pressure will be lower.
Open Impellers For open impellers, as each adjustment is made to re-establish clearance to the casing, the distance (gap) between the back of the impeller and the stuffing box will increase. A performance drop will start to occur when the gap begins to exceed 0.060 inch. The increased distance renders the pump out vanes less effective. Consequently both the stuffing box pressure and the axial thrust will increase. A good practice is to limit re-establishing clearance on an open impeller design to three times before you disassemble the pump for wear inspection.
Dealing with Dynamic Forces Pump out vanes are a design compromise consequently there is a small, but acceptable tradeoff with efficiency and power consumption. Some impellers will have both balance holes and pump out vanes, others just balance holes or just pump out vanes. 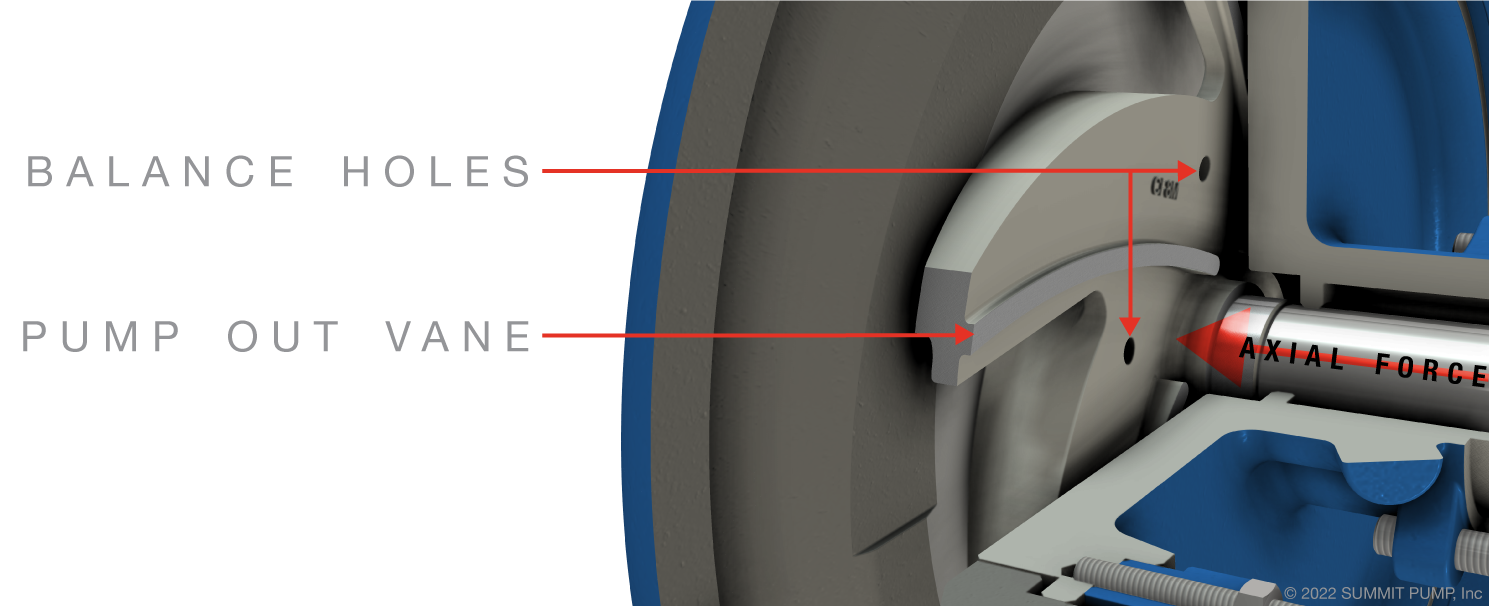 Do not use impellers with balance holes in lift situations as the potential for liquid product flashing in the seal chamber increases. Summit Pump offers reverse vane, open and closed impellers for ANSI pumps. 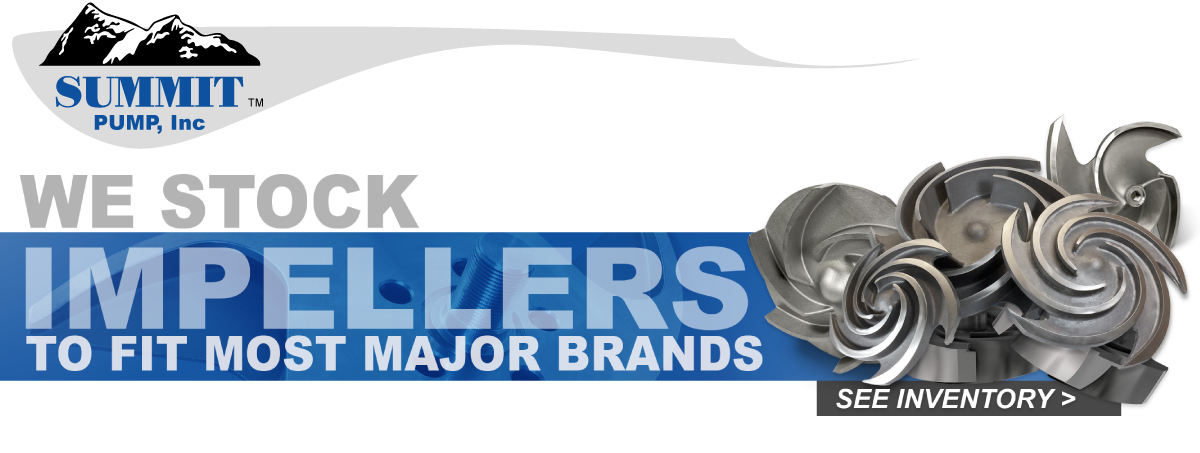 |