Dylan Thomas is a young pump technician (operator-mechanic) at the local chemical plant. One day he noticed that the batch process on unit C was taking longer than normal. He suspected something was wrong with the main pump. The pump was a horizontal ANSI type driven by an induction motor. Dillion thought back to his recent pump fundamentals training and remembered something the instructor had stated numerous times… “
The pump will operate on the published curve at the intersection of the system curve if it is able to do so”. If the pump is not operating properly, it could be due to one or several reasons.
Dylan pulled out his notes from the pump school and reviewed the list of possible causes for reduced pump performance (more on that later). After reviewing the list, Dylan remembered that he would need to measure the differential pressure across the pump and convert that result from pressure to head. Additionally he would need to check the maintenance records and pump nameplate for the correct pump size and impeller trim and download the pump curve from the manufacturer’s website.
Evaluation: Dylan checked the current differential pressure across the pump as 77 psig (178 feet). The shop maintenance records documented the pump at 85 psig (196 feet) differential when it was first installed 3 years ago.
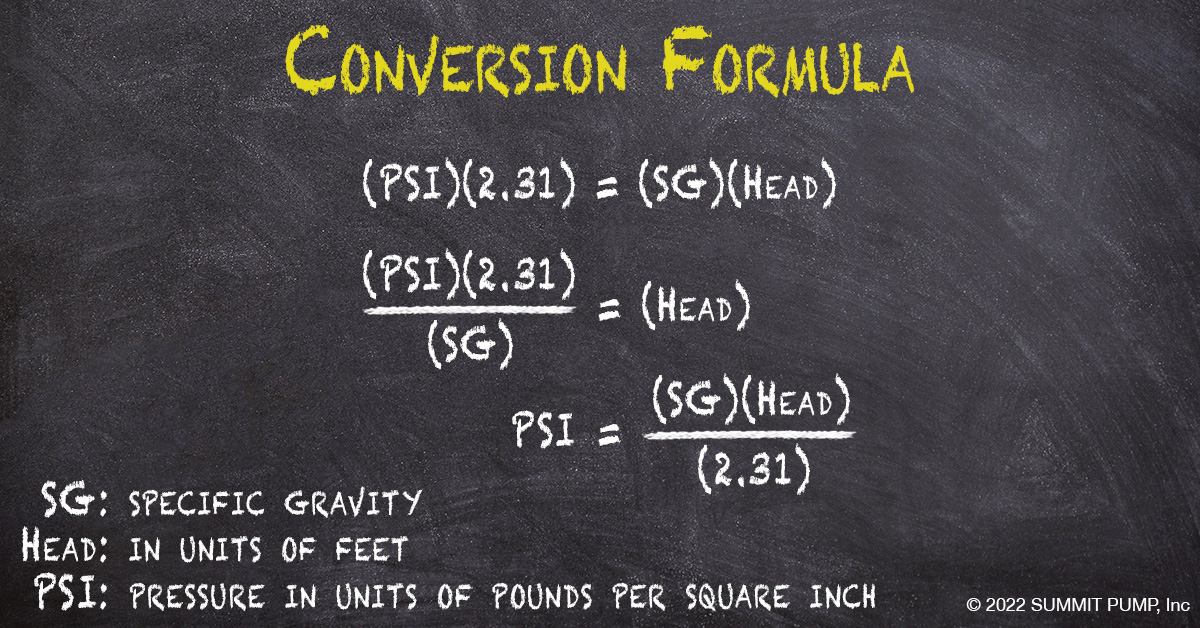
After converting the differential pressure to head, he looked over the pump curve for the hydraulic point where the pump would operate for the stated head based on the known diameter and speed. The head of 178 feet was further out and to the right on the operating curve than when the pump was new at 196 feet. The system’s flowmeter indication did not correspond to the flowrate per the pump curve. The process was taking longer so a larger flowrate didn’t make sense unless the pump was not operating on its published curve.
Diagnosis:
Utilizing the troubleshooting list, he checked the following items one at a time:
- Improper valve position… He checked the system valve lineup as correct.
- Incorrect speed… Using a strobe tachometer he confirmed the motor driver was at the correct speed.
- Net Positive Suction Head Available (Insufficient)… Dylan wasn’t sure how to calculate NPSHA but rechecked the tank level was at its normal height and he was confident that the other factors such as temperature (vapor pressure) and friction had not changed.
- Clogged suction… because of the materials, the unchanged pump suction pressure and the overall system design Dylan was fairly confident that the suction line was not clogged. He conceded it may be a remote possibility but not likely.
- Improper clearance setting… The pump clearance had been properly set years ago by the distributor’s technician. The pump had operated fine for several years.
- Direction of rotation was checked as correct.
- Change in the system curve... Based on the system materials, valve position and process cleanliness this factor was not totally eliminated but was considered a remote possibility.
- Change in the liquid properties such as viscosity or specific gravity. The company lab tech confirmed through sampling that the liquid properties had not changed.
- Pump wear… Dylan suspected this could be the most likely reason for the reduced performance and requested a pump shutdown.
Action: At the earliest opportunity Dylan scheduled the pump shut down and tagged out. Without disassembling the pump he was able to check the total axial travel of the rotating element and noted it was 0.028 inches more than when the pump was new. Dylan reset the impeller clearance in accordance with the IOM (Instruction and Operating Manual) specifications for the size/model and product temperature.
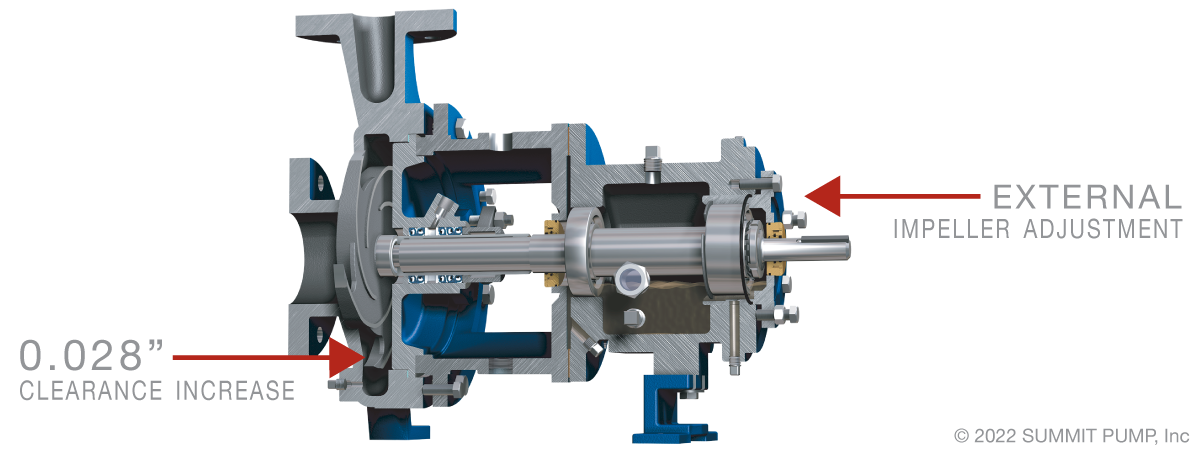
The pump was returned to service and the pressure differential returned to 85 psig. The process time for unit C returned to normal with the improved flowrate.
Conclusion: As the pump operated over the last few years the clearance between the impeller and the casing had worn by 0.028 inches. The wear occurred slowly over a long period of time and so the operators didn’t notice until the change was significant.
The wear (clearance) was enough to make the pump perform as if it was operating at a lower speed, or the impeller had been trimmed. The pump was not operating on its original published curve due to the wear, however still intersected the system curve at a lower head.