Speed is the main factor in head development for a given impeller diameter. Check that the motor/driver is operating at the correct speed. Normally not an issue, but we have witnessed problems with frequency control (remote sites that generate their own power or rogue VFD/VSD controls). A three-phase motor can also lose a phase while in operation and develop an issue that is known as
“single phasing”, which will cause a speed reduction. Other types of drives such as engines and turbines may be operating at the wrong speed due to governor issues. Belts and sheaves may also be improperly selected.
Impeller trim size is the second most common issue. A common scenario is for one party to install a small diameter impeller and later a different party sees the pump nameplate stating a larger diameter, consequently they question why the pump is not operating to the curve.
The intersection of the
system curve with the pump curve will dictate where the pump will operate on its performance curve. A common problem is when a pump is used to initially fill a system and there will be no downstream friction or static head resistance, consequently the pump will operate far right on the curve with little or no head.
A subset of the issues with system curves could be as simple as a sump level that is too low (below the pump) for the pump to lift the liquid due to friction, vapor pressure or absolute pressure issues. This is why you should always check for sufficient Net Positive Suction Head.
Air entrainment even as little as 2 % will deteriorate pump head performance. Usually by 14% the pump performance will fail. Air entrainment will typically be caused by insufficient submergence on the suction side and/or air leaks in the suction piping and/or through the packing.
Viscosity of the liquid must be accounted for and properly corrected on the pump performance curve. An increase in viscosity has a direct negative effect on the developed head. Viscosity in also directly related to the temperature. A common field issue is a system designed for warmer temperatures is started cold, which reduces the head while at the same time overloads the driver.
Don’t forget
blocked suction lines. Look for improperly positioned or failed valves and clogged suction strainers.
For most centrifugal pumps with impeller designs in the lower half of the specific speed range
reverse rotation will reduce the head a nominal 50%. If the impeller is threaded to the shaft as it is on ANSI pumps it will, 99.9% of the time, back off the shaft shoulder and attempt to friction weld itself into the casing.
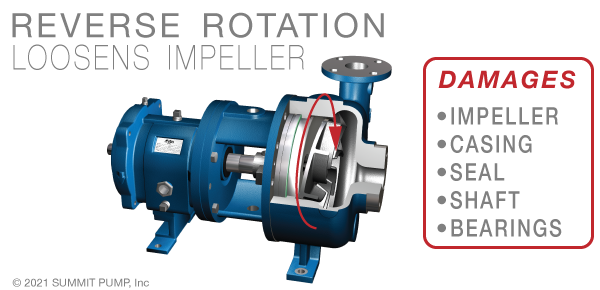
In this unsuccessful process of attempted self-removal, the process will damage the impeller, the casing, and the mechanical seal. Further it will bend the shaft and damage the bearings with all the makings of a real
Halloween nightmare.